Global Time Attack | Super Lap Battle
Track Safety Minimums
(2025 Edition)
Overview
Motorsports are inherently dangerous. These Rules are in no way a guarantee against injury or death to participants, spectators or others. You can reduce risk by driving well, properly using superior safety gear, paying attention, and reporting unsatisfactory issues to the event officials.
The entrant is responsible for ensuring that the vehicle being used is properly prepared for operation under elevated acceleration, braking and cornering forces. Drivers must have a Technical Inspection (Tech) Sheet completed, if required, and available to present to an GTA/SLB Official.
GTA/SLB Time Attack Safety Rules are divided into three (3) minimum levels of requirements, each depending on the modifications to the vehicle and potential speeds.
Although these are minimum requirements, entrants are reminded that nothing in the Rules prevents the installation of more than the minimum safety equipment. In cases where installing safety equipment may necessitate further modification not allowed by a specific competition rule set, the minimum modification necessary is permitted to perform safety equipment installation (e.g., trimming plastic cosmetic trim and carpet for roll bars, or modify door trim, windows and door structure for “NASCAR” style door bars on a roll cage, Street and Enthusiast class door panels and windows must remain and function).
Entrants are also reminded that there is a considerable gap between a minimum standard and the best protection that current technology can provide. It is recommended that seats, restraint systems, roll bars and helmets meet the highest safety standards possible.
Safety Minimums
1. Safety Level 1
It is intended that Safety Level 1 is similar to that of track events, and Time Trials vehicles running within this safety level should be streetable, and on street-appropriate tires fitting the competitors class requirements.
1.1. All Vehicles
The following requirements apply to all vehicles.
1.1.1. Seats and Seat Belts
- All vehicles must provide factory original (or better) seats that are securely mounted.
- All vehicles must have seat belts with a minimum of three (3) mounting points (if OEM using an OEM or reclining seat) mounted as originally equipped. OEM 2 point lap belts and aftermarket 4 point harnesses are not allowed.
- All vehicles running a fixed back race seat must have an SFI, FIA or equivalently rated 5 or 6 point harness with proper harness mounting, routing and wrapping.
- Shoulder harness must be attached to a cage or harness bar with a belt angle of no more than 15 degrees +/- of horizontal.
- Sub belts must be anchored center mass or behind the driver.
- Side belts must be attached to the chassis or floor side of the seat bracket unless OEM.
- Clip in belts must have safety pins or wire installed in the appropriate holes if available.
- Holes made in the chassis used for belt anchoring or seat mounting must use a load dispersing large washer with minimum SAE Grade 5 or better, 5/16-inch or 8mm minimum diameter.
- See diagram below for acceptable harness installation.
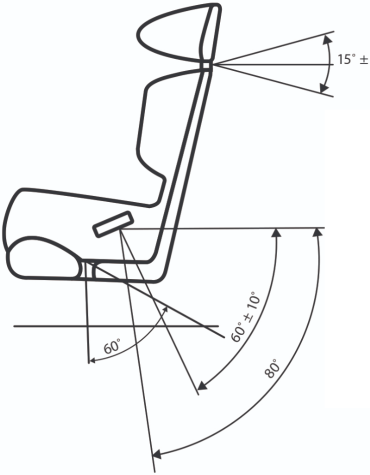
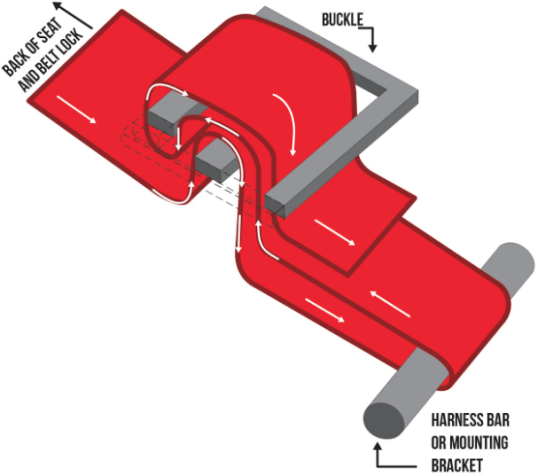
1.1.2. Interior
- The interior and trunk must be emptied and clear of all loose items, including floor mats which are not secured with clips or fasteners.
1.1.3. Brakes
It is the competitors responsibility to ensure the following:
- Brake pads or shoes should not be less than 50% worn at the start of an event and should not ever be more than 85% worn during competition.
- Brake fluid must be clean and full (DOT 4 recommended).
- Vehicles must have at least one working brake light.
- There must be no brake fluid leaks.
- Rotors and drums must be in good condition without cracks.
1.1.4. Tires and Wheels
It is the competitors responsibility to ensure the following:
- Tires must be in good condition with adequate tread. and speed rating.
- All lug nuts, wheel bolts or wheel nuts must be present and torqued to spec.
- Hub caps, or any wheel cosmetic accessory which is not positively secured by clip or fastener, must be removed.
- Wheels must not have cracks or structural damage.
1.1.5. Suspension and Steering
It is the competitors responsibility to ensure the following:
- Wheel bearings must not have play.
- Ball joints must be in good condition.
- Steering must not have excessive play.
- Shocks/Struts must not be leaking.
1.1.6. Engine and Drivetrain
It is the competitors responsibility to ensure the following:
- All fluids must be at correct levels. Fluid caps must be tight and secure, overflow containers present and there must not be any fluid leaks.
- Belts and hoses must be in good condition.
- Battery must be secured, and battery terminals covered. (Note: flexible battery hold-downs, such as bungee cords/straps, are not acceptable unless OEM.)
- Exhaust system must be properly secured and free from leaks. (There may be sound restrictions.)
- Throttle must have a quick, positive return.
1.1.7. Roll Bars
Vehicle safety must be designed in a way to allow the driver to exit the vehicle quickly in the event of an on track emergency. Drivers will be tested at the organization’s discretion to confirm they can exit the vehicle safely in a time frame of fifteen seconds or less, and must be done wearing complete safety gear and tightly harnessed into the driver’s seat when the test begins.
- When present, any part of a roll bar able to be contacted by a driver’s head must have padding.
1.1.8. Other
- Glass must not have any severe cracks in the line of sight.
- Outside and rear-view mirrors must be present(except unlimited/pro comp), when applicable, and be secure and free of cracks.
- Any video cameras/recording devices must be securely mounted.
Helmet required and must be Snell SA2010 or newer. M rated helmets may be used but not recommended.
1.2. Convertibles
It is highly recommended that all convertible vehicles be equipped with an aftermarket roll bar that meets or exceeds the standards set in the Time Trials Safety Standard Level 2. (Section 2.1.1) However, Safety Standard Level 1 requires the vehicle meets at least one of the following criteria and is not subject to any of the listed exceptions:
1.2.1. Convertible vehicles must have a roll bar which meets the Safety Level 2 standards (2.1.1.) for material and construction unless one of the following criteria is met:
- The vehicle is equipped with documented factory installed roll over protection. (Windshield frame and factory installed roll bars and/or “pop-up” bars that are designated as roll over protection.) A few examples are Audi TT, BMW 98-up 3,6,Z3/4, Corvette C6/C7, Honda S2000, Nissan 350/370Z, Porsche 911 996-up.
1.2.2. T-tops and targa top cars
- T-top and targa top cars are not considered convertibles, and do not fall under the convertible requirements.
1.3. Modified Fuel Lines/Fuel Tanks
Vehicles with aftermarket fuel tanks (e.g., fuel cells) must meet the minimum requirements for FIA FT3 or SFI 28.3 fuel cells, fuel lines and fire extinguishers outlined in Level 2 Safety minimums.
2. Safety Level 2
It is intended that Safety Level 2 be for GTA Limited Class vehicles.
2.1. All Vehicles
Vehicles running under the Safety Level 2 minimums must meet the requirements of Safety Level 1, plus the additions below.
2.1.1. Roll Bars
Vehicle safety must be designed in a way to allow the driver to exit the vehicle quickly in the event of an on track emergency. Drivers will be tested at the organization’s discretion to confirm they can exit the vehicle safely in a time frame of fifteen seconds or less, and must be done wearing complete safety gear and tightly harnessed into the driver’s seat when the test begins.
At a minimum, all vehicles running under Level 2 Safety must have a roll bar.
A roll bar is defined as a main hoop and diagonal placed behind the driver and supplemented by two braces and a horizontal harness bar at an appropriate height. The roll bar must be designed to withstand compression forces resulting from the weight of the car coming down on the roll structure, and to take fore-and-aft loads resulting from the car skidding along the ground on the roll structure. The basic purpose of the roll bar is to protect the driver in case the vehicle rolls over. Roll bars must meet the following criteria.
- One continuous length of tubing must be used for the hoop member with smooth continuous bends and no evidence of crimping or wall failure.
- The top of the roll bar must be above the top of the driver’s helmet when the driver is in normal driving position.
- The two (2) vertical members forming the sides of the hoop must be more than 15 inches apart (inside dimension), and it is desirable that it extend the full width of the cockpit.
- An inspection hole of at least 3/16 inch diameter to facilitate verification of wall thickness is required. It must be drilled in a non-critical area of each major required roll bar member at least three (3) inches from any weld or bend.
- All bolts and nuts shall be SAE Grade 5 or better, 5/16-inch or 8mm minimum diameter.
- Braces and portions of the main hoop subject to contact by the driver’s or passenger’s helmet, as seated normally and restrained by seat belt and harness, must be padded with a non-resilient material such as Ethafoam® or Ensolite® or other similar material with a minimum thickness of 1/2 inch. Padding meeting SFI spec 45.1 or FIA 8857-2001 is strongly recommended.
- The size of tubing to be used for the main hoop, braces and diagonals shall be determined on the basis of the weight of the car. The following minimum sizes are required and are based upon the weight of the car without the driver. Dimensions are nominal. 0.010- inch variation in wall thickness is allowed.

- The roll bar hoop and all braces must be of seamless or DOM mild steel tubing (SAE 1010, 1020, 1025) or equivalent, or alloy steel tubing (SAE 4130), T45 or Docol R8.
- All welding should be of the highest possible quality with full penetration. Craters should be filled to the cross section of the weld and undercut to be no more than 0.01 inch deep.
- All roll bars must be braced in a manner to prevent movement in a fore-and-aft direction with the braces attached within the top third of the roll hoop. At a minimum, two (2) braces must be used, parallel to the sides of the car, and placed at the outer extremities of the roll bar hoop. Such braces should extend to the rear whenever possible. Diagonal lateral bracing must be installed to prevent lateral distortion of the hoop. In most cases, a lateral brace from the bottom corner of the hoop on the side to the top corner of the hoop on the other side is sufficient. Although installing the diagonal lateral brace in the main hoop is the strongest alternative (and hence most preferable), there may be instances where such an installation is not practical. In such situations, the installation of the diagonal brace running from the bottom of the fore/aft brace on one side to the top corner of the hoop on the other side is acceptable. In convertible vehicles with a production line beginning 1990 or later, such as the Mazda Miata, a “V” design, also known as a “double diagonal” used between the rear supports is acceptable.
- Removable roll bars and braces must be very carefully designed and constructed to be at least as strong as a permanent installation. If one (1) tube fits inside another tube to facilitate removal, the removable portion must fit tightly and must bottom on the permanent mounting, and at least two (2) bolts must be used to secure each telescope section. The telescope section must be at least eight (8) inches in length. One (1) bolt is required if one (1) end is welded to the main hoop.
- Roll bars and braces must be attached to the frame of the car wherever possible. Mounting plates may be used for this purpose where desired.
- In the case of cars with unitized or frameless construction, mounting plates may be used to secure the roll bar structure to the car floor. The important consideration is that the load be distributed over as large an area as possible. A backup plate of equal size and thickness must be used on the opposite side of the panel with the plates through-bolted together.
- Mounting plates bolted to the structure shall not be less than 0.1875 inch thick and the use of a back-up plate of equal size and thickness on the opposite side of the panel with the plates through- bolted together is recommended. A minimum of three (3) bolts per plate is required for bolted mounting plates.
- Mounting plates welded to the structure shall not be less than 0.080 inch thick. Whenever possible the mounting plate should extend onto a vertical section of the structure, such as a door pillar.
2.1.2. Fire Suppression
- All (Street and above) vehicles shall have a device to suppress fires meeting one of the following minimum requirements:
- On-board fire Suppression systems
- Halon 1301 or 1211, two (2) pound minimum capacity by weight.
- Dry chemical fire extinguisher, two (2) pound minimum with a positive indicator showing charge. Chemical: 10 BC or 1A10BC Underwriters Laboratory rating.
- The fire extinguisher shall be securely mounted. All mounting brackets shall be metal and of the quick-release type.
- All (Street and above) vehicles shall have a device to suppress fires meeting one of the following minimum requirements:
2.1.3. Driver Restraints
All drivers shall utilize either a five- (5), six- (6) or seven-point (7) restraint harness.
- The following harness requirements must be met:
- Shoulder straps shall be separate.
- Two-inch (2) shoulder straps shall only be used with head and neck devices.
- All harnesses shall bear labels bearing either of the following SFI or FIA certifications.
- SFI specification 16.1 or 16.5
- FIA specification 8853/1985 including amendment 1/92 or FIA specifications 8853/98 and 8854/98.
- SFI and FIA harnesses are not subject to a time constraint but shall be in good condition (no cuts, abrasions, abnormal wear, etc.).
- Helmet required. Snell SA2010 or newer.
- See diagram below for acceptable harness installation.
- The following harness requirements must be met:
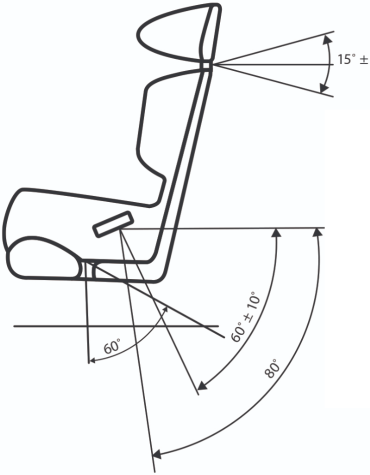
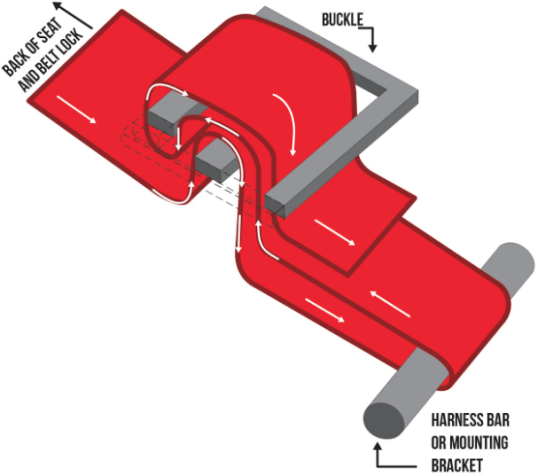
2.1.4. Seats
It is highly recommended that the driver’s seat be replaced with a one- piece, bucket-type race seat. If used, the one-piece, bucket-type race seat shall be securely mounted and provide fore/aft and lateral support.
2.2 Fuel Cells
Fuel cells must be FIA FT-3 or SFI 28.3 or higher. Mounting must be in accordance with the manufacturer’s recommendations and securely mounted. In cabin fuel lines must be of a braided, reinforced type and pressure hoses must be positively retained, crimped or threaded fittings not push-on.
2.3 Driver Attire
A driver competing in Limited, Unlimited, or Pro/Comp class is required to wear a suit that covers his or her entire body except for hands, feet, and head. It is highly recommended for all classes. Driving suits shall be one piece carrying an SFI 3.2A/1 rating or higher (3.2A/5, 3.2A/10, 3.2A/15, or 3.2A/20) or FIA 8856-2000, FIA NORME 1986/1986. The minimum driving suit requirement for vehicles using any type of diesel or diesel mixture is 3.2A/5, or higher. Note-other types of fuel may require higher ratings.
2.3.1 Underwear
Approved long underwear made of fire resistant material must be worn with all suits except those carrying a rating of SFI 3.2A/5, 3.2A/10, 3.2A/15, 3.2A/20 or FIA 8856-2000. Underwear certified to SFI 3.3 or FIA 88562000 is strongly recommended in all cases. All drivers using any type of diesel or diesel mixture must wear approved long underwear made of fire resistant material, if the suit rating is less than 3.2A/10. Note-other types of fuel may require higher ratings.
2.3.2 Helmet
All Unlimited and Pro/Comp drivers are required to wear a properly fitted and secured helmet while on track. Helmets must be approved by Snell and carry a sticker of Snell SA2010 or newer.
2.3.3 Gloves
Drivers in unlimited class shall wear gloves made from fire resistant material or leather that fully cover the hands and leave no exposed skin when worn with the driving suit.
2.3.4 Eye and Face protection
A full-face helmet with an impact resistant face shield is highly recommended for all vehicles. Eye protection is required. Face shields, safety glasses, or goggles completely made of impact resistant material are permitted as “eye protection.” However, the choice of eye protection used, and the responsibility for any failure, belongs to the driver. Drivers with beards or long hair must also wear a face cover (balaclava) made of approved fire resistant materials. A full helmet skirt made of Nomex or other fire resistant material shall also satisfy this rule.
2.3.5 Shoes
Shoes made of fire resistant material or common cowhide leather are required for Unlimited and Pro/Comp class and highly recommended for all competitors. Shoes must cover the entire foot so that there are no exposed areas of skin.
2.3.6 Socks
Socks made of approved fire resistant material must be worn.
2.3.7 Head and Neck Restraint
Use of a head and neck restraint system or device, carrying an SFI 38.1, FIA 8858-2002 or FIA 8858-2010 certification label, is mandatory.
3. Safety Level 3
It is intended that Safety Level 3 is for GTA Unlimited, international Unlimited and Pro/Comp classes.
3.1. All Vehicles
Vehicles running under the Safety Level 3 must meet the requirements of Safety Levels 1 and 2, plus the additions below.
3.1.1. Roll Cages
Vehicle safety must be designed in a way to allow the driver to exit the vehicle quickly in the event of an on track emergency. Drivers will be tested at the organization’s discretion to confirm they can exit the vehicle safely in a time frame of fifteen seconds or less, and must be done wearing complete safety gear and tightly harnessed into the driver’s seat when the test begins.
All Safety Level 3 cars must utilize a roll cage compliant with the following specifications.
These specifications apply to all vehicles competing in Unlimited or Pro-Comp classes.
- Definition: A roll cage consists of the main hoop, front hoop, side protection, and braces as specified in these Rules.
- Main Hoop
- The main hoop (behind the driver) must be the full width of the cockpit for all cars. It must be one continuous length of tubing with smooth bends and no evidence of crimping or wall failure. The main hoop must maintain a single plane.
- On all closed cars, the main hoop must be as close as possible to the roof and “B” pillars.
- On open cars retaining the windshield frame, the main hoop must be full height for the entire width of the hoop. The top of the main hoop must be at least two (2) inches above the driver’s helmet.
- Open cars without the windshield frame may use an asymmetric main hoop. The main hoop must be full width to the passenger side of the car. On the passenger side of the car, the hoop must be at least as high as the top of the rear corner of the door. The main hoop must be high enough that a straight line drawn from the top of the main hoop to the top of the front hoop would pass over the driver’s helmet and steering wheel when the driver is seated in the normal driving position. Additionally, the top of the main hoop must be at least two (2) inches above the driver’s helmet.
- Main Hoop Bracing
- Main hoops shall incorporate a diagonal brace. The brace shall either be in the plane of the main hoop or extend from the top of one rear brace to the bottom of the opposite rear brace. Automobiles with mid- mounted engines can have the lower mounting point attached to the frame of the automobile within six (6) inches of the main hoop. In the case of braces in the plane of the main hoop, the brace must span at least 50% of the width of the main hoop, and at least 75% of the height of the main hoop. In convertible vehicles with a production line beginning 1990 or later, such as the Mazda Miata, a “V” design, also known as a “double diagonal” used between the rear supports is acceptable.
- Cars must incorporate a main hoop horizontal brace at the approximate level of the driver’s shoulders but not lower than the shoulder belt mounting point. If a double-diagonal “X” brace is used in the plane of the main hoop, a half-width horizontal brace may be used behind the driver’s seat to mount the seat back and shoulder harness.
- Cars must have two (2) braces extending to the rear from the main hoop and attaching to the frame or chassis. Braces must be attached as near as possible to the top of the main hoop (not more than six (6) inches below the top), and at an included angle of at least 30 degrees.
- Open cars must have two (2) braces extending forward from the main hoop and attaching to the front hoop, not more than six (6) inches below the top of the front and main hoop. It is recommended that the front and rear braces attach to the main hoop as close as possible to each other.
- On cars where the rear window/bulkhead prohibits the installation of rear braces (e.g., Honda del Sol), the main hoop shall be attached to the body by plates welded to the cage and bolted to the stock shoulder harness mounting points. This installation design must incorporate a diagonal bar connecting the top of the main hoop to the lower front passenger side mounting point (Petty bar). Alternatively, the rear window may be removed and a clear, polycarbonate replacement installed. The rear cage braces may pass through this replacement window and through the engine cover or bodywork to allow connection to the frame or unibody.
- Front Hoop
- Roll cages may be of two designs, low front hoop or high front hoop. All closed-top cars and cars that retain the windshield frame must have a high front hoop design. Open cars may incorporate a high or low front hoop design. High front hoops are also referred to as side hoops.
- Closed cars: The front hoop (side hoop) must follow the line of the A-pillars to the top of the windshield and be connected by horizontal bars to the top of the main hoop on each side (as close to the roof as possible). Instead of a single front hoop, two side hoops (down tubes) may be used. Alternatively, a top “halo” hoop following the roof line from the main hoop to the windshield with forward down tubes following the A-pillars to the floor may be used. Regardless of which one of the two approved tubing configurations, there shall be a tube connecting the two A-pillar tubes at the top of the windshield.
- Open cars: The height of the front hoop must be consistent across the full width of the cockpit.
- Roll cages may be of two designs, low front hoop or high front hoop. All closed-top cars and cars that retain the windshield frame must have a high front hoop design. Open cars may incorporate a high or low front hoop design. High front hoops are also referred to as side hoops.
- Front Hoop Bracing
All open cars with a high front hoop and all tube frame closed cars must incorporate a horizontal front hoop brace at the approximate level of the dashboard. It is recommended production-chassis cars also have the front hoop brace.- One tube may extend, from each front down tube, forward to the firewall or through the firewall. It is recommended that this tube, one on each side, connect to the chassis at a point not more than 12 inches forward of the front axle centerline.
- Side Protection
- Side tubes connecting the front and main hoops across both door openings are mandatory. Tubes that are welded to any part of the same mounting plate are considered to be connected to one another.
- NASCAR-style side protection or one bar bisecting another to form an “X” is permitted. Door side tubes may extend into the front door.
- Main Hoop
- Definition: A roll cage consists of the main hoop, front hoop, side protection, and braces as specified in these Rules.
3.1.2. Roll Cage Attachment Points
- Production-chassis cars: The roll cage must attach to the vehicle structure within the passenger compartment in a minimum of six (6) points as specified in these Rules.
- Tube-frame cars: The roll cage shall be integrated into the frame or chassis.
- Mounting Plates
- Mounting plates welded to the structure of the car shall not be less than 0.080 inches thick and no more than 0.25 inches thick. Plates may be on multiple planes.
- The thickness of mounting plates bolted or riveted to the structure of the car must not be less than the thickness of the roll hoop or brace that they attach to the chassis and must be backed up with a plate of equal size and thickness on the opposite side of the chassis panel. Plates may be on multiple planes but shall not be greater than 15 inches on any side.
- Fasteners for bolted or riveted mounting plates must be Grade 5/Metric 8.8 or better with a minimum diameter of 5/16 inch or 8mm.
3.1.3. Roll Cage Tubing
- Seamless or DOM mild steel tubing (SAE 1020 or 1025 recommended) or alloy steel tubing (SAE 4130 or T45), or Docol R8 tubing must be used for all roll cage structures. Alloy and mild steel tubing may not be mixed. ERW tubing is not allowed.
- The following table shows the minimum allowed tubing outer diameter and wall thickness by vehicle weight:
- For purposes of determining tubing sizes, the vehicle weight is as raced without driver, fuel and ballast. The minus tolerance for wall thickness should not be less than 0.010 inch below the nominal thickness.
- The required tubing elements must meet the material minimums set forth above. Optional tubing elements may be any size.
- The minus variance of tubing wall thickness due to manufacturing tolerances is limited to 0.010 inch.
- Either an inspection hole between 3/16- and 1/4-inch diameter must be drilled in a non-critical area of the front and rear hoops, as well as one of the supplemental braces to facilitate verification of wall thickness.
3.1.4. Basic Design Considerations
- All portions of the roll cage subject to contact by the driver must be padded with a minimum 1 inch of material. Padding that meets or exceeds SFI 45.1 or FIA 8857-2001 (curved padding), or SFI 45.2 or FIA sports car headrest material (flat padding) specification is recommended.

- The radius of all bends in the roll cage (measured at centerline of tubing) must not be less than three (3) times the diameter of the tubing.
- It is recommended that all joints of the roll cage be welded. All welding must include full penetration, no cold lap, no surface porosity, no crater porosity, no cracks, no whiskers, and so forth. Welds shall be continuous around the entire tubular structure. Procedures for welding alloy steel shall be in accordance with accepted industry practice. It is recommended that a certified AWS D1.1 welder do all welding.
- It is recommended that gussets be used at all joints (Except Enthusiast and Street class cars where it is not allowed).
- Any number of additional tube elements is permitted within the boundaries of the cage structure. Such tube elements may pass through any mandatory or optional bulkhead or panel separating the driver/passenger compartment from the trunk/cargo area/fuel tank/fuel from cell area provided the bulkhead is sealed around such tube elements.
- Removable roll cage bracing is acceptable in one of the following configurations:
- If one tube fits inside another tube to facilitate removal, the removable portion must fit tightly and must bottom by design, and at least two (2) bolts must be used to secure each joint. The telescoping section must be at least eight (8) inches long. The minimum bolt diameter is 3/8 inch.
- Removable bracing may incorporate connectors of the double-lug, double ear-type, tapered or muff-type. The double-lug type must include a doubler, gusset, or capping arrangement to avoid distortion or excessive strain caused by welding. Double ear-type joints must be fully welded at all the mating surfaces.
3.1.5. Manufacturer Supplied/FIA/MSA Homologated Roll Cages
- Cars may compete with FIA or FIA-Approved Test Houses homologated cages provided the cage was built by the manufacturer or a manufacturer designated shop/team and approved for use. Cars must have the FIA identification plate attached to the cage. Also confirmation that the cage was certified by an FIA-Approved Test House.
- Cars may compete with an approved MSA (Motor Sports Association UK) Roll Over Protection System Certificate. All related engineering drawings and documents shall be submitted to GTA. Cars must have an MSA identification plate attached to the cage along with a letter certifying the cage was approved by the MSA.
3.2 Any competitor using Greater than 75% Methanol as a primary fuel must acknowledge GTA staff and have SFI 3.2A/20 approved safety gear.
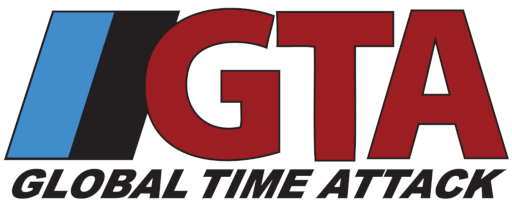
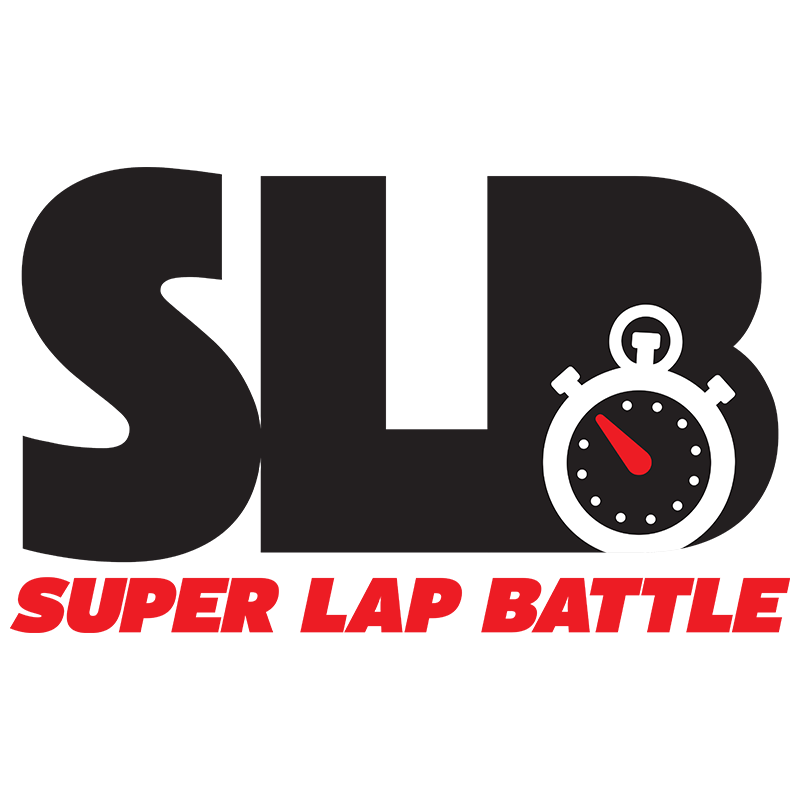